
Unlike companies which manufacture biodiesel production equipment (biodiesel processor) based on outdated, tank technologies, which have been used for over a century, our company uses the high-frequency magnetic impulse cavitation principle, previously used in classified technologies, allowing us to achieve some significant advantages:
-
Low demands on the quality of the raw oil
High-frequency magnetic impulse cavitation reactors work successfully and steadily with both raw and purified oil, and with all types of animal fats and fat mixtures with vegetable oils. This wide range of oils (sunflower oil, rapeseed oil, linseed oil, palm oil, mustard oil etc.) can be used for biodiesel fuel production with almost any acid number and it is also possible to use waste from livestock and poultry processing plants. The equipment does not need to be adjusted when the type of oil is changed. -
“One pass” reaction procedure
Unlike in outdated “tank” technologies, no re-etherification reaction is needed in magnetic impulse cavitation technology. This innovation means that the time taken to obtain biodiesel is reduced by a factor of 8-10. -
Purifying sorbates, washing and drying are not required
When using conventional technologies, it is not possible to obtain proper quality biodiesel fuel immediately. Therefore a process of impurity elimination, involving washing or purifying using sorbates, is needed. This requires additional equipment for primary biodiesel product washing (a mixture of water and alcohol is usually used for this purpose) and additional units for what is known as vacuum drying. When the cavitation biodiesel manufacture method is used there is no need for the finished product to be washed or dried, and this therefore eliminates waste water and sorbate utilization processes. -
Minimal alcohol and catalyst quantity. No alcohol recovery process
One of the main problems with “tank” technologies is the need to add, and consequently to recover, additional methanol to the reactor. This requires additional equipment and wastes electric power. In cavitation technology, the alcohol quantity used for the reaction conforms precisely to the stochiometric composition, i.e. the minimum volume. There is no need for a re-etherification reaction. The use of expensive and dangerous equipment for methanol recuperation is excluded from the process. Any inevitable alcohol losses during recovery are eliminated, which improves the environmental conditions and explosion-proof characteristics. -
Minimum energy consumption
Conventional biodiesel production methods are based on heating the oil to 67-70 °C. This involves significant electric power costs; in addition, the methanol recovery process (required when the reaction is carried out using conventional technologies), additional re-etherification and also vacuum dehydrating lead to considerable electric power consumption. The use of cavitation processing eliminates all the stages mentioned above, which means that 5-7 times less electric power is used. -
Low-temperature reaction
In high-frequency magnetic impulse cavitation, processing takes place in the reactor on molecular level. All components are exposed to magnetic-directed cavitation pulses. Fatty acid molecules are split using micro-explosions; this results in a decrease of viscosity, a cetane number increase, an improvement in the energetic parameters of the future fuel and a considerable acceleration and improvement of the etherification reaction quality. It must be noted that the reaction takes place at room temperature and there is no need to heat the oil. -
Minimal overall module dimensions
Our automatic modules take up 5-10 times less floor space than conventional equipment of a similar capacity.
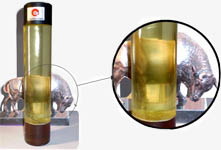
BIODIESEL MADE OF ANIMAL FAT
Biodiesel derived from animal fat (waste from the processing of livestock) using the cavitation reactor PULSAR-CT. Animal fat was first liquefied (heated up to 60°C). Source components ratio: Animal fat – 5350 ml; Methanol – 700 ml; Catalyst (potassium methylate) – 50 g; Processing time – 50 seconds; Separation time (gravity method) – 20 minutes
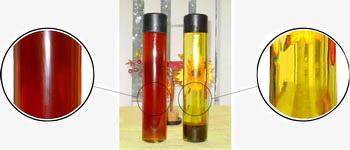
BIODIESEL MADE OF CRUDE SUNFLOWER OIL
The picture shows the source oil (crude non-refined sunflower oil) and the result of source product treatment in the cavitation reactor PULSAR-CT. Test conditions: Crude sunflower oil – 7000 ml; Methanol – 900 ml; Catalyst (potassium methylate) – 65 g; Processing time – 50 seconds; Separation time (gravity method) – 20 minutes
FULLY AUTOMATIC MODULES FOR BIODIESEL PRODUCTION
BioSMART-CT 1…16
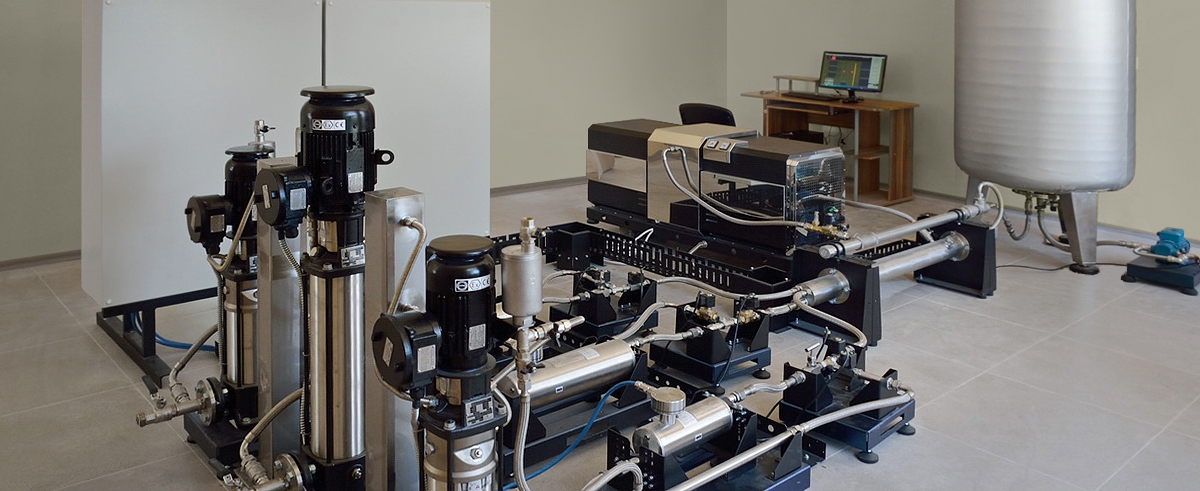
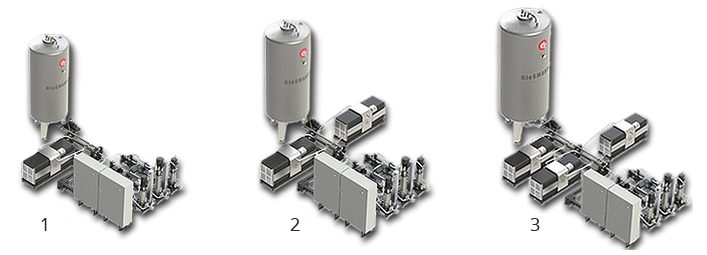
Our company has developed new modules for biodiesel production BioSMART-CT based on new cavitation processors PULSAR-CT 730. Eleven types of the BioSMART-CT modules allow to process from 1 up to 16 cubic meters of oil per hour. Extremely precision system of initial products dosing based on Coriolis principle, new high-effective cavitation reactors, reliable separation system proven over the years, original user-friendly software – all these make BioSMART the most modern and effective unit in the world market of biodiesel production.For building our BioSMART we collaborate only with the most well-known and reliable companies such as Grundfos, Siemens, Schneider Electric, Moeller, Fanuc etc. Powerful PLC control all parameters of the production process such as mass flow rates, temperatures in the processors, separation process, power consumption, outlet flow rate etc. and monitor the work of all mechanisms. Operators need only to enter data of initial products to the computer and press the button START, the rest will be done by the BioSMART. All the mechanisms are ATEX certified to ensure the safety of the whole system while working with explosive liquids such as methanol and catalyst. BioSMART works in continuous operating mode and do not require an interference of the operator except some extraordinary situations. BioSMART will inform the operator about all errors, if it occurs during processing, and give tips how to fix the problem. BioSMART maintains records of the consumed products quantities and working time. BioSMART can process any kinds of oils or blends of different oils including used cooking oil and do not require special pretreatment of oil except simple mechanical filtration. Biodiesel washing, drying and methanol recovery are not required. This considerably reduces the time of biodiesel production and electric power consumption in comparison with traditional old-fashioned technologies. The degree of BioSMART automation has been developed to the maximum rate, that allows to avoid “human factor” in the production of biodiesel and as a consequence of this considerably shortens the possibility the operator’ errors. BioSMART can be operated by operator with basic technical training and minimal level of PC knowledge. BioSMART are intended for twenty-four-hour work and do not require special servicing
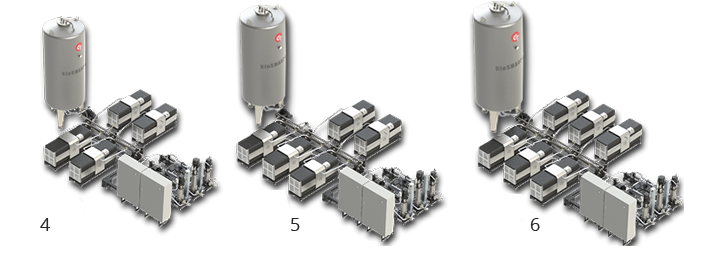
PRODUCTS FAMILY
Minimal productivity, liter per hour |
Quantity of cavitation processors PULSAR-CT 730
|
Rated power, KW | Floor space*, L×W, m2 | |
BioSMART-CT 1 |
1 000
|
1
|
32
|
3×3.7
|
BioSMART-CT 2 |
2 000
|
2
|
63
|
3×3.7
|
BioSMART-CT 3 |
3 000
|
3
|
94
|
4×3.7
|
BioSMART-CT 4 |
4 000
|
4
|
125
|
4×3.7
|
BioSMART-CT 5 |
5 000
|
5
|
156
|
5×3.7
|
BioSMART-CT 6 |
6 000
|
6
|
187
|
5×3.7
|
BioSMART-CT 08 |
8 000
|
8
|
270
|
7×4
|
BioSMART-CT 10 |
10 000
|
10
|
330
|
8×4
|
BioSMART-CT 12 |
12 000
|
12
|
395
|
9×4
|
BioSMART-CT 14 |
14 000
|
14
|
455
|
10×4
|
BioSMART-CT 16 |
16 000
|
16
|
515
|
11×4
|
* Floor space is indicated without separation tank
AUTOMATIC MODULES BIOTRON-CT
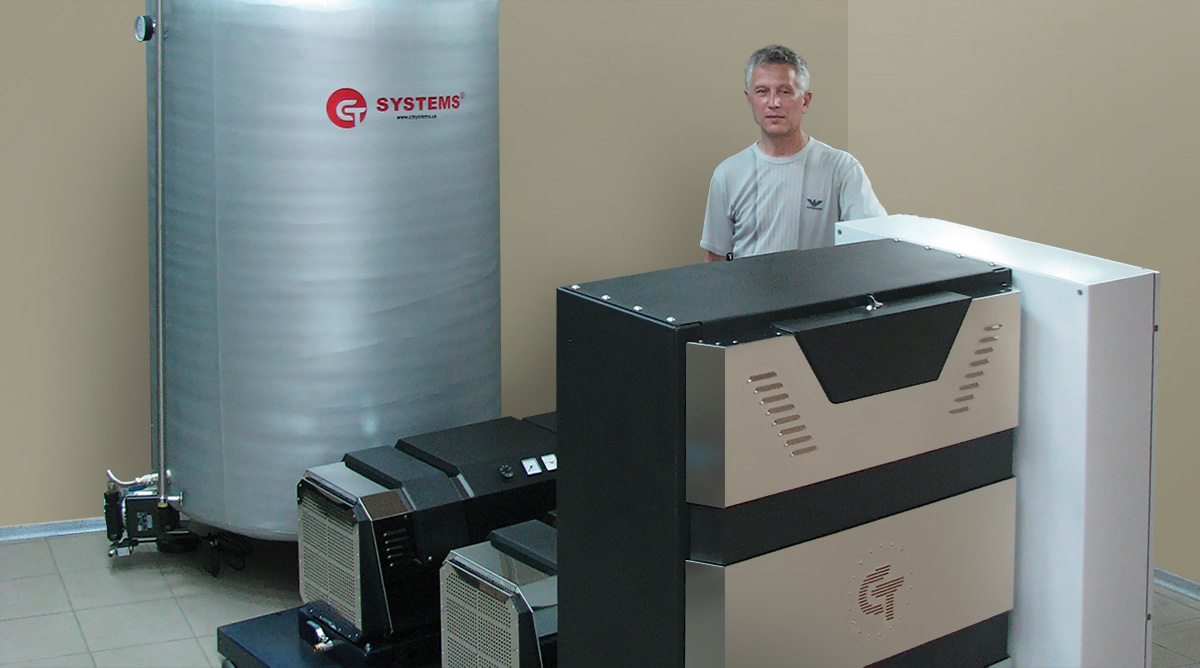
BIOTRON-CT 150
|
BIOTRON-CT 500
|
BIOTRON-CT 1000
|
|
Capacity (rated), liters per hour |
150-200
|
500-700
|
1000-1200
|
Rated power, kW |
5.4
|
16
|
32
|
Weight (approximately), kg |
540
|
765
|
975
|
Maximum allowed liquid temperature in module, °C |
90
|
90
|
90
|
Automation level |
ultimate
|
ultimate
|
ultimate
|
Operation mode |
continuous
|
continuous
|
continuous
|
Processing efficiency, kW hour/liter |
0.032
|
0.032
|
0.032
|
Capacity adjustment |
yes
|
yes
|
yes
|
Processed liquid special requirements |
no
|
no
|
no
|
Floor space occupied with one module, sq.m. |
2.8
|
3.0
|
4.0
|
Overall dimensions (L x W x H), mm |
2000х1393х1980
|
2316х1393х2500
|
2515х1484х2700
|
Explosion proof certificates |
ATEX
|
ATEX
|
ATEX
|
BIOTRON-CT 150-S
|
BIOTRON-CT 500-S
|
BIOTRON-CT 1000-S
|
|
Capacity (rated), liters per hour |
150-200
|
500-700
|
1000-1200
|
Rated power, kW |
5.4
|
16
|
32
|
Weight (approximately), kg |
460
|
575
|
780
|
Maximum allowed liquid temperature in module, °C |
90
|
90
|
90
|
Automation level |
semi
|
semi
|
semi
|
Operation mode |
continuous
|
continuous
|
continuous
|
Processing efficiency, kW hour/liter |
0.032
|
0.032
|
0.032
|
Capacity adjustment |
yes
|
yes
|
yes
|
Processed liquid special requirements |
no
|
no
|
no
|
Floor space occupied with one module, sq.m. |
2.0
|
2.0
|
3.0
|
Overall dimensions (L x W x H), mm |
1435х1393х1411
|
1435х1393х1411
|
1430х1484х1411
|
Explosion proof certificates |
ATEX
|
ATEX
|
ATEX
|
DEMONSTRATION OF THE BIOTRON-CT
AUTOMATIC MODULES «BIOTRON-CT» CONSIST OF THREE MAIN UNITS:
1. PULSAR-CT THIRD-GENERATION MAGNETIC IMPULSE REACTORS (Biodiesel Processor)
PULSAR-CT is a third-generation hydrodynamic high-frequency magnetic impulse cavitation reactor – state-of-art technology in biodiesel fuel production. A very high level of reliability, modern design, process automation, stable results with any oil types, minimum power consumption – all of these features make PULSAR-CT cavitators the undisputed leader in high-tech biodiesel fuel production. PULSAR-CT cavitation reactors are the core elements of BIOTRON-CT automatic biodiesel production modules.

PULSAR -CT 715
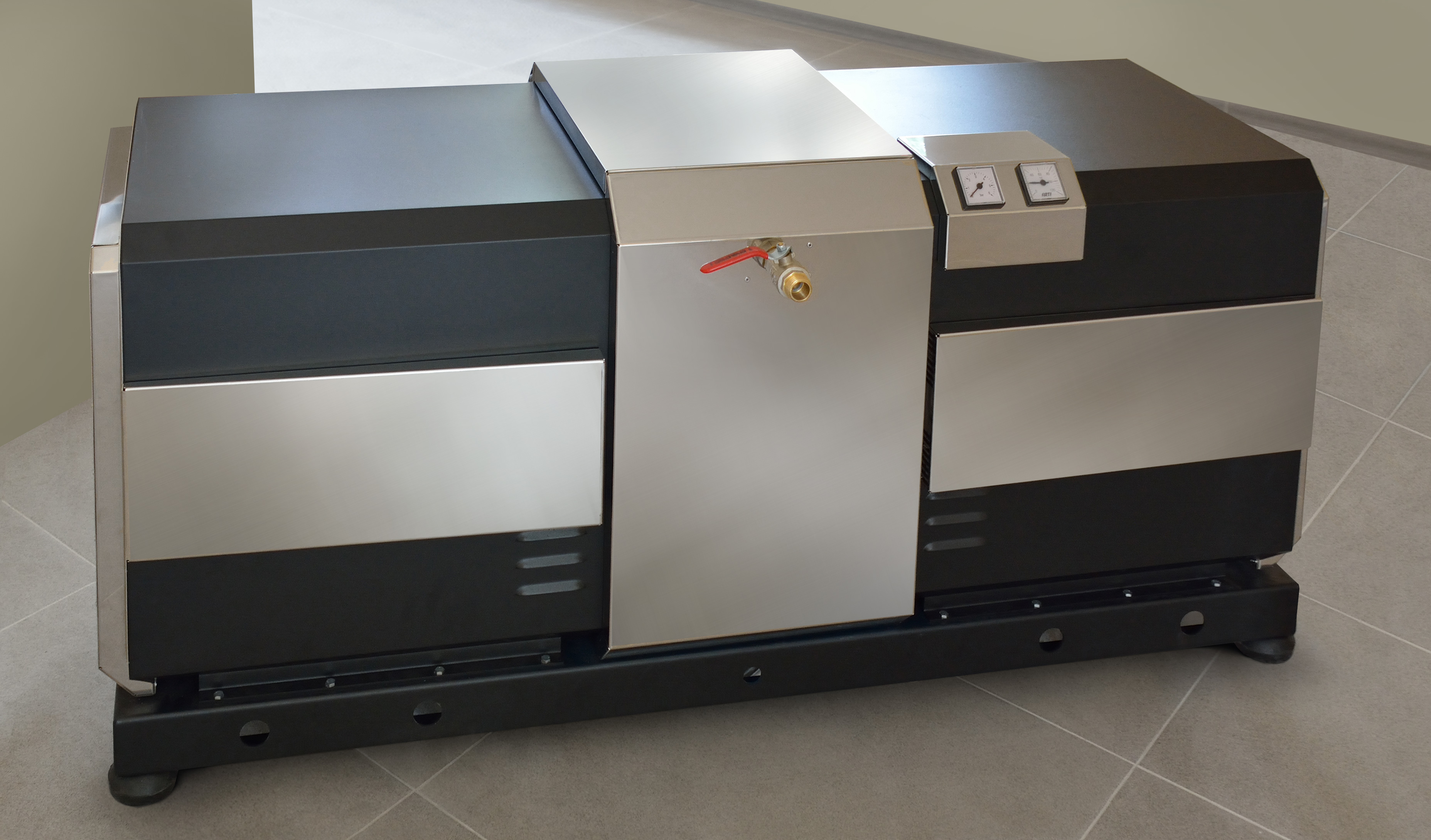
PULSAR -CT 730
Technical parameters
PULSAR-СT 805
|
PULSAR-СT 715
|
PULSAR-СT 730
|
|
Capacity (rated), liters per hour |
150
|
500
|
1000
|
Rated power, kW |
4.4
|
15
|
30
|
Weight, kg |
79
|
235
|
405
|
Operation mode |
continuous
|
continuous
|
continuous
|
Processing efficiency, kW hour/liter |
0.03
|
0.028
|
0.028
|
Flow rate adjustment |
yes
|
yes
|
yes
|
Overall dimensions (L x W x H), mm |
800х400х420
|
1050х450х550
|
1490х560х675
|
2. PPS-CT 1200: ELECTRONIC SYSTEM FOR THE PRELIMINARY DOSING AND PROCESSING OF SOURCE PRODUCTS
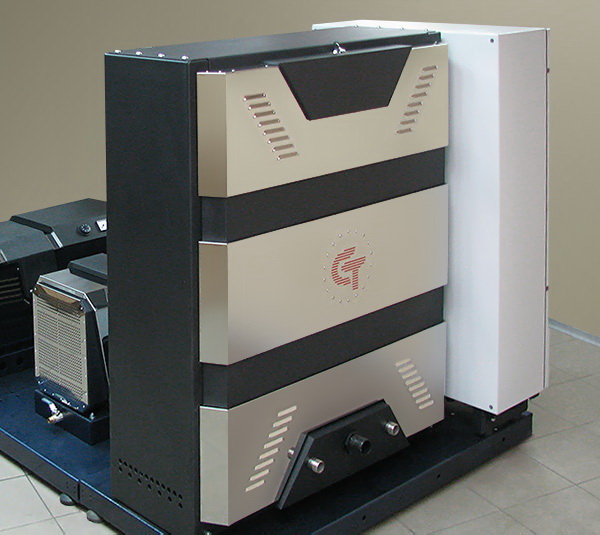
PPS-СT 1200
Technical parameters
PPS-CT 1200
|
|
Capacity (rated), liters per hour |
1200
|
Number of components mixed |
3
|
Rated power, kW |
2
|
Explosion proof certificates |
ATEX
|
Automation level |
Fully automatic
|
Modern dosing systems, used by other companies are not able to guarantee the steady dosing of source ingredients if ambient conditions (temperature, liquid level in source ingredients and prepared products tanks, oil viscosity, etc.) change. The system which our company has designed does not include these disadvantages and has an extremely high dosing precision – 0.1%. In addition, the system is equipped with a pre-mixing unit, there is the option of adjusting flow rate and pressure at the system output and there is also a source components dosing feature. The equipment uses original software and high-reliability electronics produced by the company FANUC. The PPS-CT 1200 system also includes a biodiesel fuel production safety tracking function. The processor tracks the source component availability, their filling speed, mixing intensity, ability to pass through pipelines and valves, etc. If there is an emergency, the processor will stop the whole system; send an audible signal to operator and show the error code on the display, together with a detailed description and possible causes. In this way, for example, if there is an oil shortage in the source products storage, the following message will be displayed:
3. ELECTRONIC TRACKING SYSTEM OF THE FILLING, SEPARATION AND DISCHARGE OF FINISHED PRODUCTS
Our automatic unit contains the separation process tracking system in order to eliminate the human factor in biodiesel availability evaluation (“by-sight”). The supersensitive sensors monitor the state of the glycerol and biodiesel in the separation tank. Data obtained by the sensors is transferred to the computer, which evaluates the readiness of the source products and also controls biodiesel and glycerin discharge from the separation tanks to the finished product storage. The entire process takes place in continuous mode. If any unforeseen situation occurs, and, for any reason, the separation does not take place or takes place at a poor speed, the computer will stop the entire system and send a signal to the operator about the need to analyze and correct the situation. For more information about the operation of the separation process tracking system please see the animated presentation.
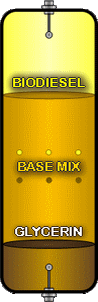
USER-FRIENDLY INTERFACE SOFTWARE, WHICH DOES NOT REQUIRE THE OPERATOR TO HAVE SPECIAL SKILLS
All processes which take place in the automatic module are controlled by the microprocessor. The interface that our software team has developed is very simple and self-explanatory. The operator is able to control the whole system just by clicking a mouse button. In the adjustment mode, the operator can control any module mechanism separately, set the necessary sensor response value, etc. In the automatic mode, just click the START button – the BIOTRON-CT system will do the rest itself. One computer can serve up to five BIOTRON-CT automatic modules at once. Software and electronic components are designed based on the software and electronic components produced by the Japanese company FANUC, one of the world market leaders in this area.
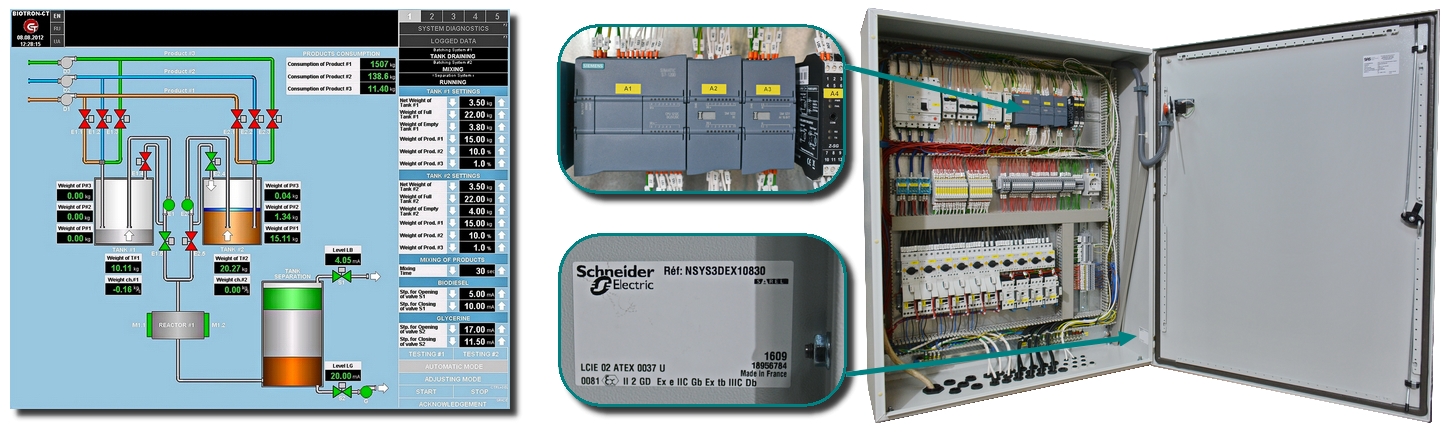
PRODUCTS FAMILY
Automatic equipment
|
Semi-automatic equipment
|
|||
BIOTRON-CT500
|
BIOTRON-CT1000
|
BIOTRON-CT500-S
|
BIOTRON-CT1000-S
|
|
Capacity (rated), liters per hour |
500
|
1000
|
500
|
1000
|
Rated power, kW |
16
|
32
|
16
|
32
|
Overall dimensions (L x W x H), mm |
2200х1400х2300
|
2900х1400х2300
|
1400х1400х1350
|
2100х1400х1350
|
Weight, kg |
700
|
1100
|
375
|
650
|
The number of modules that can be mounted together into one hyper-productive complex is practically unlimited. This allows flexible, high-technology biodiesel production of any capacity to be achieved. One operator is able to control one complex,
The number of modules that can be mounted together into one hyper-productive complex is practically unlimited. This allows flexible, high-technology biodiesel production of any capacity to be achieved. One operator is able to control one complex, which consists of number of modules.